The Buzz on Alcast Company
The Buzz on Alcast Company
Blog Article
Our Alcast Company Diaries
Table of ContentsThe Alcast Company PDFsThe 10-Minute Rule for Alcast Company9 Simple Techniques For Alcast CompanyNot known Details About Alcast Company Get This Report on Alcast CompanyA Biased View of Alcast Company
The refined difference depends on the chemical content. Chemical Comparison of Cast Aluminum Alloys Silicon advertises castability by decreasing the alloy's melting temperature and improving fluidity throughout casting. It plays an important role in enabling complex mold and mildews to be filled accurately. Furthermore, silicon contributes to the alloy's toughness and wear resistance, making it beneficial in applications where toughness is critical, such as auto components and engine components.It likewise enhances the machinability of the alloy, making it easier to refine right into finished items. In this method, iron contributes to the total workability of aluminum alloys.
Manganese contributes to the stamina of aluminum alloys and improves workability (aluminum casting company). It is typically made use of in functioned aluminum items like sheets, extrusions, and profiles. The visibility of manganese aids in the alloy's formability and resistance to cracking throughout construction processes. Magnesium is a light-weight component that provides stamina and effect resistance to aluminum alloys.
The Definitive Guide for Alcast Company
Zinc boosts the castability of aluminum alloys and helps manage the solidification procedure throughout spreading. It improves the alloy's strength and hardness.

The main thermal conductivity, tensile toughness, yield stamina, and prolongation differ. Select appropriate raw products according to the performance of the target product created. Amongst the above alloys, A356 has the highest thermal conductivity, and A380 and ADC12 have the most affordable. The tensile restriction is the opposite. A360 has the most effective return toughness and the highest possible prolongation price.
An Unbiased View of Alcast Company
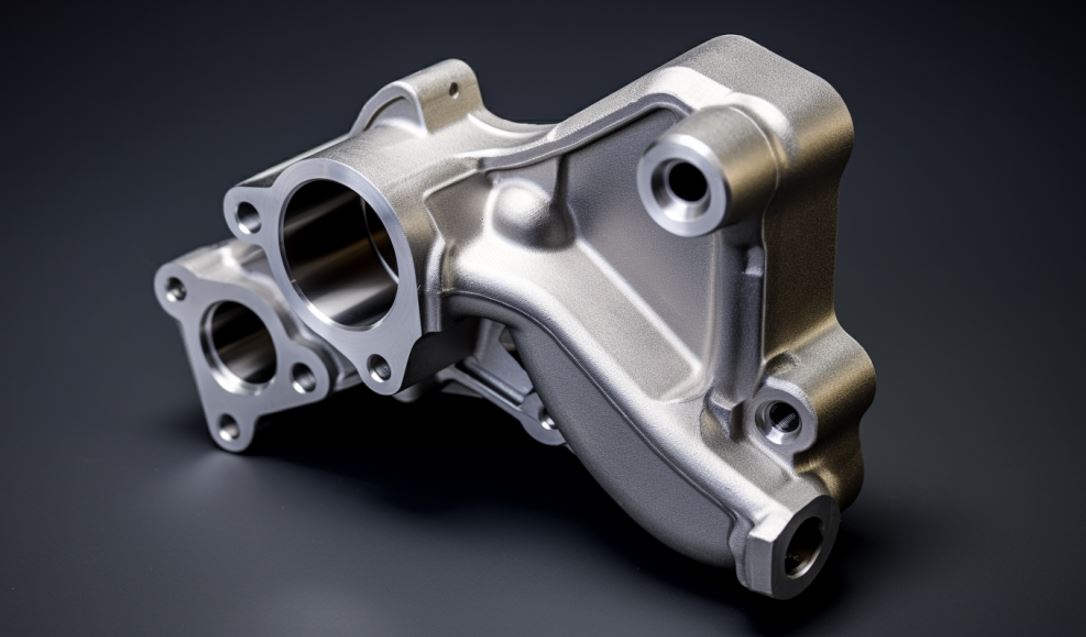
In precision casting, 6063 is appropriate for applications where intricate geometries and high-grade surface coatings are critical. Instances include telecommunication rooms, where the alloy's superior formability enables sleek and visually pleasing layouts while maintaining structural honesty. Similarly, in the Illumination Solutions sector, precision-cast 6063 components produce classy and efficient illumination components that require complex shapes and great thermal performance.
It brings about a finer surface finish and far better corrosion resistance in A360. The A360 shows superior elongation, making it perfect for complicated and thin-walled elements. In precision casting applications, A360 is well-suited for industries such as Customer Electronic Devices, Telecommunication, and Power Devices. Its improved fluidness permits elaborate, high-precision elements like mobile phone coverings and interaction tool real estates.
More About Alcast Company
Its unique homes make A360 a beneficial option for accuracy casting in these markets, enhancing product resilience and top quality. Aluminum alloy 380, or A380, is an extensively made use of spreading alloy with several distinct attributes. It provides superb castability, making it an optimal selection for precision spreading. A380 exhibits excellent fluidity when molten, making certain detailed and detailed mold and mildews are accurately duplicated.
In accuracy spreading, light weight aluminum 413 radiates in the Customer Electronics and Power Equipment industries. It's typically used to craft elaborate components like smartphone real estates, electronic camera bodies, and power device coverings. Its accuracy is exceptional, with limited resistances approximately 0.01 mm, ensuring perfect item setting up. This alloy's superior corrosion resistance makes it an outstanding option for outside applications, ensuring resilient, durable products in the mentioned sectors.
Alcast Company for Dummies
The light weight aluminum alloy you choose will considerably impact both the casting process and the homes of the last item. Due to the fact that of this, you must make your decision very carefully and Recommended Reading take an enlightened strategy.
Identifying the most appropriate aluminum alloy for your application will suggest considering a large variety of qualities. The very first category addresses alloy characteristics that affect the production procedure.
Everything about Alcast Company
The alloy you choose for die spreading straight impacts several facets of the casting procedure, like just how easy the alloy is to deal with and if it is susceptible to casting flaws. Hot cracking, additionally known as solidification cracking, is a regular die casting problem for aluminum alloys that can result in internal or surface-level rips or fractures.
Certain light weight aluminum alloys are much more vulnerable to hot fracturing than others, and your choice should consider this. An additional common flaw found in the die spreading of aluminum is pass away soldering, which is when the actors sticks to the die walls and makes ejection tough. It can harm both the cast and the die, so you must look for alloys with high anti-soldering buildings.
Corrosion resistance, which is already a significant feature of aluminum, can differ considerably from alloy to alloy and is a necessary particular to consider depending on the environmental conditions your product will be subjected to (Aluminum Casting). Wear resistance is an additional residential or commercial property frequently looked for in light weight aluminum products and can separate some alloys
Report this page